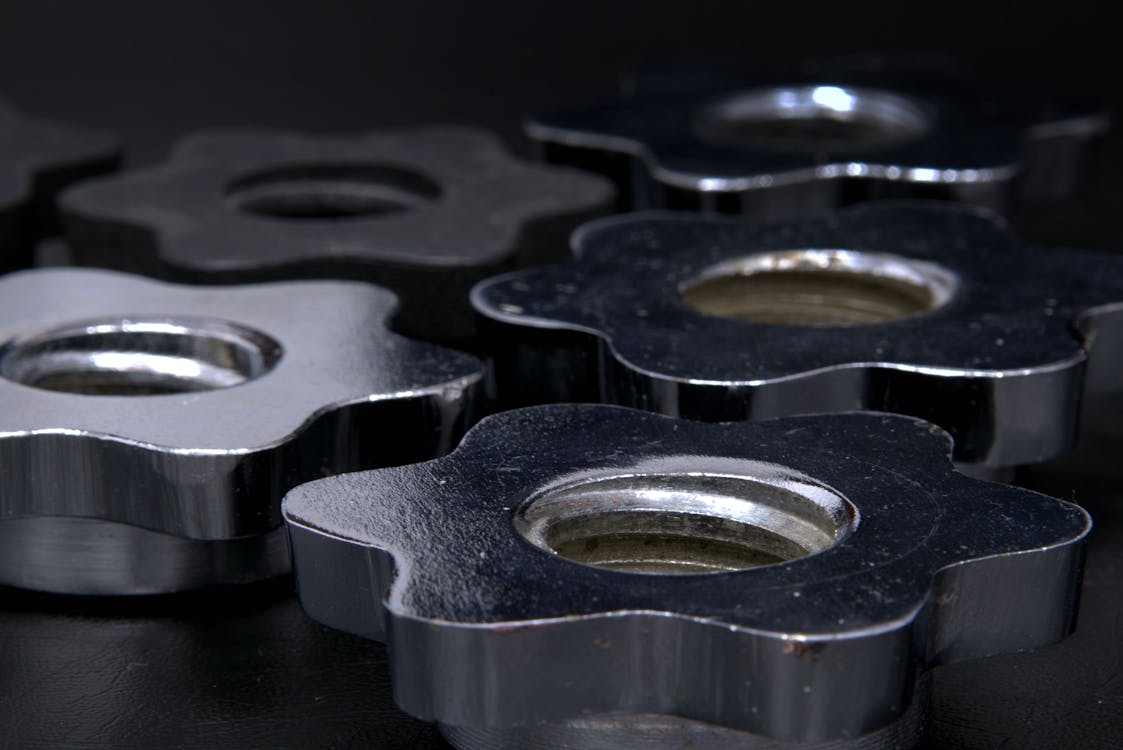
Chassis and Body Parts Design
In this first post we will be discussing some general ideas about 2D conception of the mechanical parts of the platform.
At the start of any project, especially mechanical ones we tend to translate the project requirements into sketches. These sketches define the major design headlines and the raw conception of your individual parts’ design and how they are to fit together in the assembly. For sketching purposes, we use SketchBook by Autodesk. The app was recently published full and completely free, suffice to log in with your Autodesk ID and you are good to go.
We identify the different pre-made parts that will fit into our design, in our case the SoC computing board, the motors, the electronics, the batteries and the wheels. These consists the building blocks of our design and they decide the minimum dimensions requirements for any chassis parts we may conceptualize further down the road.
The first concept and tip we would like to present to you is the idea of real scale dimensioning. As many makers or hobbyist may have already experienced, ordering your parts online may be deceiving by making assumptions about these parts’ real dimensions through the product’s pictures. To overcome this problem, one might proceed to real world scaling by either: Using a caliper: by opening it to the greatest dimension of the part in question, this action should give you a feel of what to expect in terms of real size. Lengths of cardboard: using cardboard pieces cut to dimensions will help you have a broader idea on the volume of the part and help you brainstorm designs that may fit it perfectly.
To tackle final CAD conception of the platform parts, we use either Catchbook App from Siemens(R) to have a quick dimensioned drawing for the parts. For advanced scaled 2D CAD designs, the perfect free choice is DraftSight by Dassault Systemes.
The second concept and tip we would like to introduce is Bounding Boxes: By creating boxes with length*width you can effectively figure out the layout of the different parts you are using for your build.
The first step into the design process would be to create the design area, this is the outermost extents of your platform; for our design a 500*500 square made up the whole area the platform will cover. After defining the real-estate we have at our disposal, we might either proceed to defining bounding boxes for each part directly on the software or building some to-scale cardboard pieces of our parts and brainstorming the general layout and design consequences of the choices we take.
The third concept is relative dimensioning: On the Catchbook app, drawings are not to scale, but the drawing is nonetheless relatively scaled; equivalent to say that dimensions are proportional to each other but not to the absolute scale.
After figuring out the relative dimensions of all the building blocks, and their layout against the major design area, we might proceed to scaled 2D CAD design. On DraftSight or any software of choice for your case. We start replicating the major dimensions for the layout as we conceptualized it. From these drawings we have the starting point to define and scale our chassis parts.
After defining the parts in question, we can group and copy them to separate file for print and machining later on.
Check out the YouTube channel video for intro to Catchbook, DraftSight and how to best use them.
05 Comments




Emilly Blunt
December 4, 2017 at 3:12 pm
Never say goodbye till the end comes!